|
0%
Abstract: Frostytech departs from the usual pixel fodder for a brief look at some cooling technologies you have never seen before. We touch on some fun tests from the unpublished Frostytech archives and collect all the thermodynamics research we've reported on into one location.
|
Home >
Reviews >
Page: Annex B) Diamond, Nano-structure and Metal Foam Heatsinks
|
Chemical Vapor Deposition Diamond Heat
Spreaders :
Ever wonder what the next generation cooling
technologies are for cooling next generation processors? Chemical Vapor
Deposition Diamond surfaces is one. Diamond is applied to silicon
processors to improve surface thermal conductivity substantially according
to this report from the University of Maryland. Of course the high cost of
producing diamond heatspreaders means that more economical alternatives
like Electroless Nickel, with a thermal conductivity of 90.7 W/m/K, could
also work.
Other exotic cooling technologies mentioned in the
VITA report include;
- Heat Pipes
- Liquid Cooling
- Spray Evaporative Cooling
- Chip Refrigeration (Phase Change Cooling)
- Cryogenic Cooling
- Thermoelectric Cooling
- Non-Metallic Microchannels
- Meso / Micro Cold Plates
|
Fraunhofer Institute's 100 µm-density heat
exchanger:
The Fraunhofer Institute for
Manufacturing and Advanced Materials (IFAM) has
pioneered metal fiber structures, along with hollow spheres structures and
metal foams. In the case pictured below, Direct Typed structures are
printed with gas atomized 316L stainless steel. Given the right design,
you could be looking at some of the worlds best potential heat exchangers
here...
"A printable suspension of metal powder and a binder
is pressed in a screen printing process through a computer generated mask,
followed by a hardening step. In the next step a layer-on-layer printing
is repeated until a 3-dimensional part is manufactured. A first heat
treatment is applied to remove the organic binder; subsequently the
remaining metal powder is sintered to structures with high precision and
good mechanical stability. The residual minimal wall thickness and channel
width amounts about 100 µm. In contrast, the maximal structure height may
add up to a couple of centimeters. Hence, exceedingly high aspect ratios
are feasible.
The method enables the production of 3-dimensional
structures with horizontal apertures or closed channels."
|
Tamagawa Zigzag Heatsink Fin Concept:
Tamagawa, a Japanese metal products
company, has developed a very unique heatsink fin concept for what it
calls 'advanced cooling' situations. The heatsink fins are formed into a
zigzag pattern, composed of offset micro squares stacked on top of one
another to form fins about 10-30mm tall.
The surface area and complex flow patterns that would result from such
complex interlocking fins may possibly produce a very efficient thermal
shape for increasing heat dissipation in limited spaces. We would expect
that high-volume forced air cooling would be used to combat the pressure
drop.
Shown are two examples of Tamagawa's 'zigzag' cast
aluminum and cast copper heatsink concepts. The copper prototype measures
just 40x20x10mm in size, the aluminum model appears to be somewhat larger.
|
Injection Molded Copper from Amulaire:
Most aluminum heat sinks exist as extrusions
that allow intricate shapes in only two dimensions. "By injection molding
copper, though, engineers have more control over the intricate shapes on a
heat sink," said Ken Kaskoun, VP of Sales and Marketing at Amulaire
Thermal Technology. "Molded copper lets us increase the amount of metal
over the chip and then taper off the base thickness at the heat-sink edges
or we can create an airfoil to increase air flow across an area," said
Kaskoun. The molding process also lets customers include mounting features
without the need for machining. To create a molded-copper heat sink,
Amulaire simulates a design and then machines one or two
prototypes."
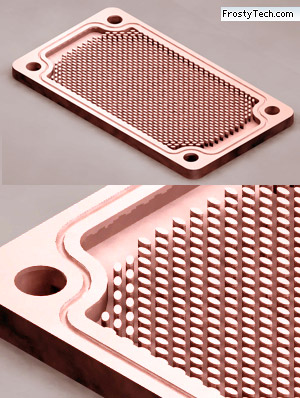
"Unlike plastic, you cannot inject
molten copper into an intricate mold. Instead, Amulaire Thermal
Technology combines fine copper with a polymer binder and injects the mix
into the mold. "The part comes out of the mold with the consistency of
chocolate," said Ken Kaskoun, VP of Sales and Marketing at Amulaire. It
then goes into a sintering oven that drives off the binder and leaves the
fused copper behind. The design shrinks uniformly by about 20 percent as
it goes from the molded to the sintered state, said Kaskoun. "After
sintering, we have a copper part that has 98 percent of the density of
solid copper." |
|
|
1:
Cryo Tech and New Cooling Technologies You Have Never Seen
2:
Thermoacoustic Cooling
3:
Phase Change Waterchilling
4:
Conduction PCB Cooling via Cold Plate Heat Exchangers
5:
The Stirling Cycle Cryo Cooler
6:
Annex. A) Graphite, Carbon Foam/Fiber, Polymer Heatsinks
7:
Annex A) Graphite, Carbon Foam/Fiber, Polymer Heatsinks
8:
Annex B) Diamond, Nano-structure and Metal Foam Heatsinks
9: — Annex B) Diamond, Nano-structure and Metal Foam Heatsinks
10:
Annex C) Heat Exchangers, Microchannel, Capilliary, Spray Watercooling
11:
Annex C) Heat Exchangers, Microchannel, Capilliary, Spray Watercooling
12:
Annex C) Heat Exchangers, Microchannel, Capilliary, Spray Watercooling
13:
Annex D) Computational Fluid Dynamics and Innovative Heatsink Tech
List all FrostyTech heat sinks that Frostytech tested?
|
|
|
|
 |
Websites you may also like:
PCSTATS
|
|
 |