|
0%
Abstract: Frostytech departs from the usual pixel fodder for a brief look at some cooling technologies you have never seen before. We touch on some fun tests from the unpublished Frostytech archives and collect all the thermodynamics research we've reported on into one location.
|
Home >
Reviews >
Page: Annex A) Graphite, Carbon Foam/Fiber, Polymer Heatsinks
|
Maxtal Graphite Heatsink Material - 450w/m·k:
Maxtal Carbon Tech Co. Ltd. produce highly thermally
conductive Graphite for a variety of uses, with conductivity reaching as
high as 450W/m-K in the X-X,Y-Y axis. "High thermal conductivity graphite
is a new conductivity and heat sinks material which has the high thermal
conductivity, big specific heat capacity, good heat stability, small
coefficient thermal expansion and corrosion resistant, etc. The material
itself has the strong air sink characteristics (cross-ventilation
ability)." |
Carbon nanofibre forest cuts thermal resistance:
NASA is using carbon nanotubes to cut thermal resistance, aiming to
improve heat flow between chips and heatsinks. Li’s alternative uses a
form of nanotube called carbon nanofibres in the interface. With two
[plain] pieces of silicon, the interface resistance is about 2cm²K/W which
can be improved with grease or solder. People are shooting for less than
0.5cm²K/W; and 0.2 for the next generation. We can achieve 0.2 already and
it is under-optimised.”
The NASA
interface relies on the incredible thermal conductivity of carbon
nanotubes. “There is a lot of interest in this thermal conductivity. There
is literature to say it is as high as diamond. But it is highly
anisotropic,” said Li. Along the length of the tube it has diamond-like
thermal conductivity, but heat does not pass into the side of the tube
easily. “If nanotubes are packed together like spaghetti, thermal
conductivity is very poor. |
IG-430 Graphite-Copper Heatsink Research:
In this PDF by W.Y. Maeng from the Korean Atomic Energy Research
Institute, the author discusses a novel heatsink fabricated from
graphite brazed to a copper baseplate for a proton accelerator. The one
step brazing process for the joining of Cu-graphite plate uses TiCuSil
alloy. There is some interesting cooling technology being discussed here,
but keep in mind that while Graphite has a relatively good thermal
conductivity it is generally only in one plane). This research note goes on to test IG-430 graphite
impregnated with Cu and Ag alloys.
"The graphite used for front facing material is IG-430 of
Toyo Tanso. The copper plate for the cooling jacket material is made with
OHFC (Oxygen Free High Conductivity Copper, ASTM B170 Grade 1). The filler
material for the brazing is TiCuSil alloy (4.5%Ti-27.7%Cu-68.8%Ag, Wesgo
Metals)." |
Nanotubes act as 'thermal Velcro' to reduce computer-chip
heating:
"Engineers have created carpets made of tiny cylinders called carbon
nanotubes to enhance the flow of heat at a critical point where computer
chips connect to cooling devices called heat sinks, promising to help keep
future chips from overheating. Researchers are trying to develop new types
of "thermal interface materials" that conduct heat more efficiently than
conventional materials, improving overall performance and helping to meet
cooling needs of future chips that will produce more heat than current
microprocessors.
The materials, which are sandwiched between silicon chips and the metal
heat sinks, fill gaps and irregularities between the chip and metal
surfaces to enhance heat flow between the two. Purdue University
researchers have made several new thermal interface materials with carbon
nanotubes, including a Velcro-like nanocarpet. Recent
findings have shown that the nanotube-based interfaces can conduct
several times more heat than conventional thermal interface materials at
the same temperatures. The nanocarpet, called a "carbon nanotube array
thermal interface," can be attached to both the chip and heat sink
surfaces." |
Super Carbon Foam Heat Exchangers:
Copper is so last year, the new material du jour is Super
Carbon Foam. Here are a couple examples of carbon foam heat
exchangers from the company CFoam.
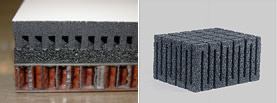
"There has been significant research activity on developing carbon foam
heat exchangers primarily because of their potential weight savings and
high efficiency. Carbon foam heat exchangers are predicted to weigh 50%
less than conventional high-temperature, metallic core pre-cooler/heat
exchanger designs, and are also expected to have twice the efficiency of
traditional heat exchangers.
CFOAM, because of its high structural strength, is a
viable material for use on helicopters, aircraft and ships. CFOAM’s significantly
higher strength allows greater flexibility in the heat exchanger fin
and core designs which cannot be obtained with the weaker pitch-based
products." |
|
|
1:
Cryo Tech and New Cooling Technologies You Have Never Seen
2:
Thermoacoustic Cooling
3:
Phase Change Waterchilling
4:
Conduction PCB Cooling via Cold Plate Heat Exchangers
5:
The Stirling Cycle Cryo Cooler
6:
Annex. A) Graphite, Carbon Foam/Fiber, Polymer Heatsinks
7: — Annex A) Graphite, Carbon Foam/Fiber, Polymer Heatsinks
8:
Annex B) Diamond, Nano-structure and Metal Foam Heatsinks
9:
Annex B) Diamond, Nano-structure and Metal Foam Heatsinks
10:
Annex C) Heat Exchangers, Microchannel, Capilliary, Spray Watercooling
11:
Annex C) Heat Exchangers, Microchannel, Capilliary, Spray Watercooling
12:
Annex C) Heat Exchangers, Microchannel, Capilliary, Spray Watercooling
13:
Annex D) Computational Fluid Dynamics and Innovative Heatsink Tech
List all FrostyTech heat sinks that Frostytech tested?
|
|
|
|
 |
Websites you may also like:
PCSTATS
|
|
 |