|
0%
Abstract: Frostytech departs from the usual pixel fodder for a brief look at some cooling technologies you have never seen before. We touch on some fun tests from the unpublished Frostytech archives and collect all the thermodynamics research we've reported on into one location.
|
Home >
Reviews >
Page: Annex D) Computational Fluid Dynamics and Innovative Heatsink Tech
|
Annex D) Computational Fluid Dynamics and Innovative Heatsink Tech
CFD and Waterblock Flow Optimizations
: An interesting read on Advanced Power Electronics Thermal Design
here, especially the part about optimizing the design of a
water block for better flow dispersal using CFD software. Here's an
excerpt;
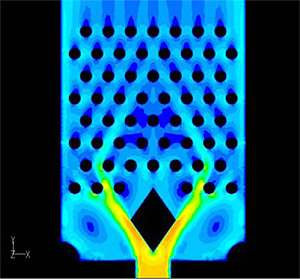 NREL
report: "Figure 1 shows the velocity distribution in the current
design. A nominal design coolant flow rate of 10 l/min is used to generate
the resulting flow field. CFD analysis shows how the incoming flow
impinges on the diamond boss and causes the flow to split into two major
streams. These narrow streams then impinge directly on the pin fins in the
first few rows. Because of the high impingement velocity at the diamond
boss, the flow attaches to the sidewalls of the boss and a substantial
portion of the flow is diverted around the interior pin fins. The CFD
analysis predicts two large re-circulation regions at the entry and a
large wake downstream of the boss. Consequently, the analysis shows that a
major portion of the coolant bypasses most of the interior fins and flows
along the two straight unobstructed channels along the sidewalls, thereby
decreasing the heat exchanger effectiveness and increasing its thermal
resistance in the inverter cooling design. This inevitably causes IGBT
temperatures to increase."
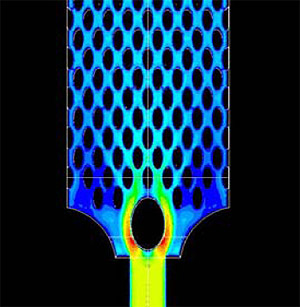 "Figure 2 illustrates that the flow around the boss now
remains attached and smoothly distributes to the fins downstream. The
reduction in the flow channel width at entry allows the flow to diffuse
out more gradually. The presence of partial fins along the sidewalls as
projections into the channel prevents the flow from bypassing the fins. A
more uniform distribution of the flow velocity is apparent in this figure.
Closer examination of the flow field reveals that the regions of flow
separation behind the mounting bosses and fins are reduced substantially
from the original design. The flow maintains a high velocity adjacent to
the sidewalls of the pin. Both these features will keep the flow channel
swept of potential debris and minimize the tendency for fouling." |
Furukawa Hexagonal Crimped Fin Heatsink Prototype
:
This prototype heatsink comes to Frostytech by Furukawa
Electric Co., Ltd., and looks to be the makings of
a next generation socket 775 cooler. Called the 'Hexagonal Crimped Fin'
heatsink, it has a thermal resistance of just 0.246 K/W. Whether this
signals the retirement of AVC's stock bifurcated fin heatsink model
currently being used of the Pentium 4 is anyone's guess.
The authors of a report on this heatsink document several
prototypes which failed to out-perform the standard socket 775 Intel
bifurcated fin in their attempt to advance crimped fin heatsinks.
The hexagon-shapped copper core was selected as it was the
only shape able to meet the mechanical needs of the crimping process for
all 132 fins (each 0.3mm thick, in pairs), and final circular shape
requirements. The bend in each set of fins 2/3's of the way out is meant
to maintain geometry between each the tips. |
Corona driven air propulsion for cooling of
electronics :
This research paper explores the viability of Corona
Driven Air Propulsion for electronics cooling. It's the first I've heard
of such an application, although the method seems fairly similar to some
piezoelectric methods in a couple respects. Read the 4-page PDF on
Corona Air Propulsion here.
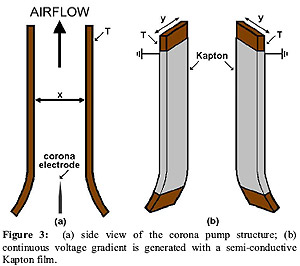
Washington.edu: "The possibility of building a
high voltage electrostatic air pump for cooling of microelectronics is
investigated. Heat sink fins are packed more closely to increase the heat
exchange surface area, resulting in narrower channels between the fins.
Air viscosity in narrow channels reduces the cooling efficiency of the
heat sinks. Electrostatic air propulsion methods may improve airflow
patterns in narrow channels. Several prototypes of the electrostatic air
pump were built. Corona onset voltage was measured, and the
current-voltage relationship showed a positive exponential relationship.
The performance of the corona pump displayed a nearly linear voltage-air
velocity relationship, a logarithmic decrease in air gap impedance between
corona and collector electrodes, and a departure from classic air velocity
profiles."
|
That's all for now, Frostytech will update this article in the future as more
curious technology surfaces from the archives. Feedback is
welcome, as are tips about new cooling technologies.
|
|
1:
Cryo Tech and New Cooling Technologies You Have Never Seen
2:
Thermoacoustic Cooling
3:
Phase Change Waterchilling
4:
Conduction PCB Cooling via Cold Plate Heat Exchangers
5:
The Stirling Cycle Cryo Cooler
6:
Annex. A) Graphite, Carbon Foam/Fiber, Polymer Heatsinks
7:
Annex A) Graphite, Carbon Foam/Fiber, Polymer Heatsinks
8:
Annex B) Diamond, Nano-structure and Metal Foam Heatsinks
9:
Annex B) Diamond, Nano-structure and Metal Foam Heatsinks
10:
Annex C) Heat Exchangers, Microchannel, Capilliary, Spray Watercooling
11:
Annex C) Heat Exchangers, Microchannel, Capilliary, Spray Watercooling
12:
Annex C) Heat Exchangers, Microchannel, Capilliary, Spray Watercooling
13: — Annex D) Computational Fluid Dynamics and Innovative Heatsink Tech
List all FrostyTech heat sinks that Frostytech tested?
|
|
|
|
 |
Websites you may also like:
PCSTATS
|
|
 |